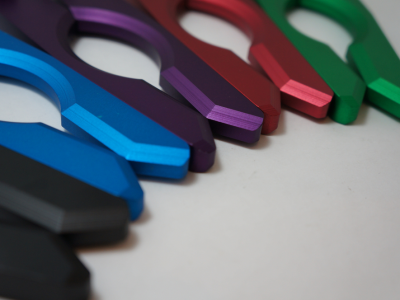
COLORATION DE MÉTAL
L’aluminium possède une couche d’oxyde naturel. Elle se forme par elle-même. L’anodisation est un procédé qui permet de contrôler l’épaisseur de cet oxyde et alors de l’utiliser pour protéger le métal contre l’oxydation.
De plus, il est possible de colorer le métal avec des pigments de couleur en utilisant les propriétés de la couche d’oxyde. Anodisation Québec possède une certaine variété de couleurs. Il ne suffit que de s’informer afin de savoir lesquelles sont disponibles; il est possible de faire des colorations selon la demande des clients.
PÉNÉTRATION DE L'OXYDE
Lors de l’anodisation, l’oxyde pénètre dans le métal. La pénétration de l’oxyde varie selon l’alliage, mais habituellement il y a une pénétration de 35 % et un gonflement de 65 %. Il est important de savoir que cet effet est inévitable lors du traitement.
La couche d’oxyde permet une meilleure résistance à l’abrasion, car l’oxyde d’aluminium possède une dureté de 200 à 350 Vickers (20 à 36 HRC).
1 : épaisseur initiale de la couche anodique
2 : début de la formation des pores
3 : pénétration de la couche d’oxyde et croissance
4 : état final de la couche
COLORATION
Le procédé de coloration est une opération supplémentaire et facultative. Il consiste à l’immersion de la pièce anodisée dans une solution contenant un colorant. Ainsi, la pièce prend la couleur désirée. Le seul moyen pour décolorer la pièce est de détruire la couche d’oxyde.
La photo de droite montre les différentes couleurs offertes. Elles ne sont pas toutes disponibles, mais il est possible de les commander.
PROPRIÉTÉS ÉLECTRIQUES |
---|
Résistivité Pour une couche non hydratée de 50 microns |
4 x 10E15 ohms cm2/m à 20 °C |
8 x 10 E15 ohms cm2/m à 100 °C |
Tension de claquage 20 à 40 volts/micron |
ANODISATION STANDARD
L’aluminium possède toujours une couche d’oxyde naturel sur sa surface. Le procédé d’anodisation permet de contrôler l’épaisseur de cet oxyde et alors de l’utiliser pour protéger le métal contre l’oxydation. De plus, il est possible de colorer le métal avec des pigments de couleur en utilisant les propriétés de la couche anodique. Anodisation Québec possède une certaine variété de couleurs. Il ne suffit que de s’informer afin de savoir lesquelles sont disponibles.
COMPOSITION DE L'OXYDE
L’oxyde est formé de 2 couches : une appelée barrière et l’autre poreuse. La couche barrière possède une épaisseur d’environ 15 nanomètres et la couche poreuse forme le reste. Les épaisseurs obtenues en anodisation varient de
6 à 25 microns.
La couche d’oxyde se forme lorsque les ions d’oxygène de la solution rencontrent les ions d’aluminium à l’interface métal/électrolyte. Plus la couche d’oxyde gagne en épaisseur, plus il sera difficile de l’augmenter davantage. L’oxyde formé se présente sous forme de cellules hexagonales ayant un pore au centre. Lors de la coloration, les pigments de couleur se retrouvent dans ces pores
RÉSISTANCE À LA CORROSION
Le traitement d’anodisation sert à augmenter la résistance à la corrosion. Le revêtement anodique qui recouvre la pièce protège le métal contre l’atmosphère oxydante.La couche d’oxyde produite respecte les normes MIL-A-8625F.
PROPRIÉTÉS À HAUTE TEMPÉRATURE
Il est possible d’utiliser les pièces anodisées à haute température, mais puisque le coefficient de dilatation de la couche d’oxyde est environ 5 fois plus petit que celui de l’aluminium, il est recommandé de faire des augmentations de température successives. Lors du refroidissement de la couche, il faut suivre les mêmes recommandations. Voici quelques propriétés thermiques de la couche anodique :
PROPRIÉTÉS À HAUTE TEMPÉRATURE |
---|
Coefficient de dilatation linéaire 5x10E-6 au lieu de 23x10E–6 de l’aluminium |
Conductibilité thermique 21 à 63 W/m°C entre 0 et 60 °C au lieu de 220 W/m°C pour Al |
POROSITÉ DE LA COUCHE
Puisque la couche d’oxyde est poreuse, elle peut alors être utilisée comme couche permettant une meilleure adhérence de revêtement sur la pièce. L’application de colle ou de peinture peut être faite. Les molécules de ces produits s’inséreront dans les pores de la couche pour permettre une meilleure adhérence.
RÉPONSE DES ALLIAGES À L'ANODISATION À L'ACIDE SULFURIQUE
Alliages de la série 1000
(aluminium pur)
Ils répondent bien au procédé. Les couches sont d’autant plus transparentes que le métal est pur. Pour obtenir un aspect intéressant, il faut éviter la présence du fer et du silicium, même à de faibles teneurs.
Alliages de la série 2000
(aluminium-cuivre)
Le cuivre en présence dans cette série va se dissoudre lors de l’anodisation et causer par la suite une coloration peu esthétique. La résistance à la corrosion sera moins importante. Le cuivre se retrouve dans les particules de seconde phase du métal et lors de sa dissolution, il empêche de recouvrir le précipité d’oxyde. De plus, la résistance à l’abrasion sera mauvaise vu la non-uniformité de la couche d’oxyde.
Alliages de la série 3000
(aluminium-manganèse)
L’anodisation de ces alliages se fait bien, mais au-delà de 1 %, les couches épaisses sont moins appropriées pour l’esthétique. La présence de manganèse provoque une couleur indésirable gris-brun. Ainsi, lors du procédé de coloration, celle-ci s’additionnera au traitement et affectera son esthétique.
Alliages de la série 5000
(aluminium-magnésium)
L’anodisation de ces alliages se fait très bien. Jusqu’à une teneur de 3 % en magnésium, les couches sont relativement claires. Pour des teneurs plus élevées, la couche prend une couleur grisâtre, parfois jaunâtre si le métal possède de faibles teneurs en manganèse ou en chrome. Ces changements de couleur sont liés à l’indice de réfraction de la couche qui est affecté par la présence de certains éléments dans le métal.
Alliages de la série 6000
(aluminium-magnésium-silicium)
Ces alliages s’anodisent bien et il est aussi possible d’obtenir de bons résultats lors de la coloration. Des traitements d’homogénéisation adaptés permettent d’obtenir une structure métallurgique très régulière, en particulier par rapport à la taille et à la répartition des précipités de seconde phase. Ces derniers influencent directement l’aspect final du métal après satinage (aspect mat) et anodisation. Lors d’anodisation de grande épaisseur (40 microns), la couche d’oxyde prend une couleur gris foncé.
Alliages de la série 7000
(aluminium-zinc)
Les alliages qui contiennent du cuivre en quantité importante (exemple : l’alliage 7075) posent quelques problèmes lors de l’anodisation, car ils réagissent de la même manière que les alliages faisant partie de la série 2000. En revanche, les nuances qui contiennent peu de cuivre seront bien adaptées à l’anodisation à l’acide sulfurique (exemple : l’alliage 7020).
AUTRES PARAMÈTRES QUI INFLUENCENT LA QUALITÉ DE L'ANODISATION
Dans les cas où une pièce d’aluminium est coulée en moule de sable ou a subi un traitement de surface au sable, l’esthétique du procédé de coloration ne sera pas maximale. Il faut éviter une trop grande présence de silicium pour obtenir une anodisation de qualité et une couleur uniforme.
D’autres impuretés peuvent influencer la qualité de la couche d’oxyde. Avant l’anodisation, il faut être sûr qu’il n’y a plus d’huile sur les pièces d’aluminium. Dans le cas contraire, la couche ne pourra se former. De plus, la présence d’huile contaminera les bassins et affectera les autres pièces.
ANODISATION DE DIFFÉRENTS ALLIAGES
Chaque type d’alliage ne répond pas de la même manière à l’anodisation. Lors de l’anodisation, il faut traiter des lots de mêmes alliages pour réussir à obtenir un bon contrôle de l’épaisseur. Il faut toujours bien identifier les alliages pour éviter la confusion dans les bassins.
EFFET DES HÉLICOÏLS OU INSERTS
La présence d’hélicoïl ou d’insert différent du matériel de base dans un alliage va contaminer les bains. Les traitements effectués par la suite seront de mauvaise qualité. Ainsi, il faut enlever ces pièces avant anodisation.
DÉFAUTS QUI APPARAISSENT LORS DE L'ANODISATION
La microstructure
Tous les métaux cristallins possèdent une microstructure qui est propre au traitement qu’ils ont subi. Lors du traitement, le métal est mis en contact avec des solutions agressives qui peuvent faire ressortir cette microstructure.
Les points de contact
Pour anodiser une pièce, il est essentiel d’avoir des points de contact sur la pièce. Ceux-ci servent à transférer l’électricité à la pièce pour que l’anodisation puisse se produire. L’oxyde ne se formera pas sur ces points et il sera possible de voir des points blancs. Toutefois, les points de contact sont choisis afin de préserver l’esthétique des pièces.
La couleur
Lorsqu’une même couleur est désirée pour un ensemble de pièces du même alliage, il est important de le spécifier. D’un traitement à l’autre, il y a toujours de petites variantes dans le procédé et cela cause de légères différences de couleur.
Note : Il sera normal d’avoir une légère variation de couleur pour de grosses commandes.
Les porosités
Les différents traitements de surface que peuvent subir des pièces peuvent cacher certains défauts du métal. Les irrégularités de surface qui ont été polies mécaniquement peuvent ressurgir à la suite de l’anodisation. Après les premières étapes de l’anodisation, ces défauts réapparaissent et affecteront la qualité du procédé de coloration. Ainsi, il y a présence de petits points blancs sur la surface après le procédé final. La photo suivante montre l’effet de la réapparition des défauts :
Les soudures
Lorsque des pièces sont soudées, elles ont subi un traitement thermique important qui change la microstructure du métal. Ce changement affectera la couleur de la couche anodique. Ainsi, les différences de couleur entre l’aluminium et les soudures seront apparentes.
La photo 1 montre une pièce soudée. Cette pièce est ensuite anodisée (photo 2). Il est possible de voir que la soudure est plus foncée que la pièce. De plus, la zone ayant subi un effet thermique est un peu plus blanche. Sur la photo 3, la pièce a été colorée. Encore une fois, il est possible de remarquer que la couleur n’est pas uniforme au pourtour et dans la soudure.
ENTRETIEN DES PIÈCES ANODISÉES
Un entretien périodique des surfaces anodisées est essentiel pour enlever les accumulations de saleté ou de dépôts. De plus, un bon entretien évitera l’apparition de taches sur les pièces. Il ne faut pas utiliser n’importe quelle technique de nettoyage, car si un produit non adéquat est utilisé, cela peut endommager la couche anodique.
Voici un tableau qui décrit les bonnes techniques d’entretien :
L’utilisation de tampons abrasifs grossiers (exemples : paille de fer ou papier émeri), de produits nettoyants très forts (détergents pour lave-vaisselle et pour la lessive) et de produits basiques ou acides abîmera la couche d’alumine. L’oxyde d’aluminium est stable pour des pH entre 5 et 10. Pour des valeurs de pH excédant cet intervalle, l’oxyde sera attaqué.
TYPE DE PROBLÈME | PRODUIT | PROCÉDURE |
Dépôt de poussière | Eau chaude et savon, ou détergent | Bien essuyer l’excès d’eau avec un tissu propre pour éviter les dépôts de sels calciques |
Dépôt gras | Solvant organique (ex. : kérosène) |
Rincer la surface au solvant propre avec un chiffon et sécher pour éviter les coulures |
Important dépôt de saleté ou suies | Abrasifs légers et eau |
Nettoyer, rincer et sécher la surface |
Dépôt ou tache résistants | Tampons abrasifs fins et eau | Frotter doucement, enlever les fibres métalliques, rincer et sécher |